The Essence of Manufacturing Project Management: Benefits, Stages, Tips & Examples
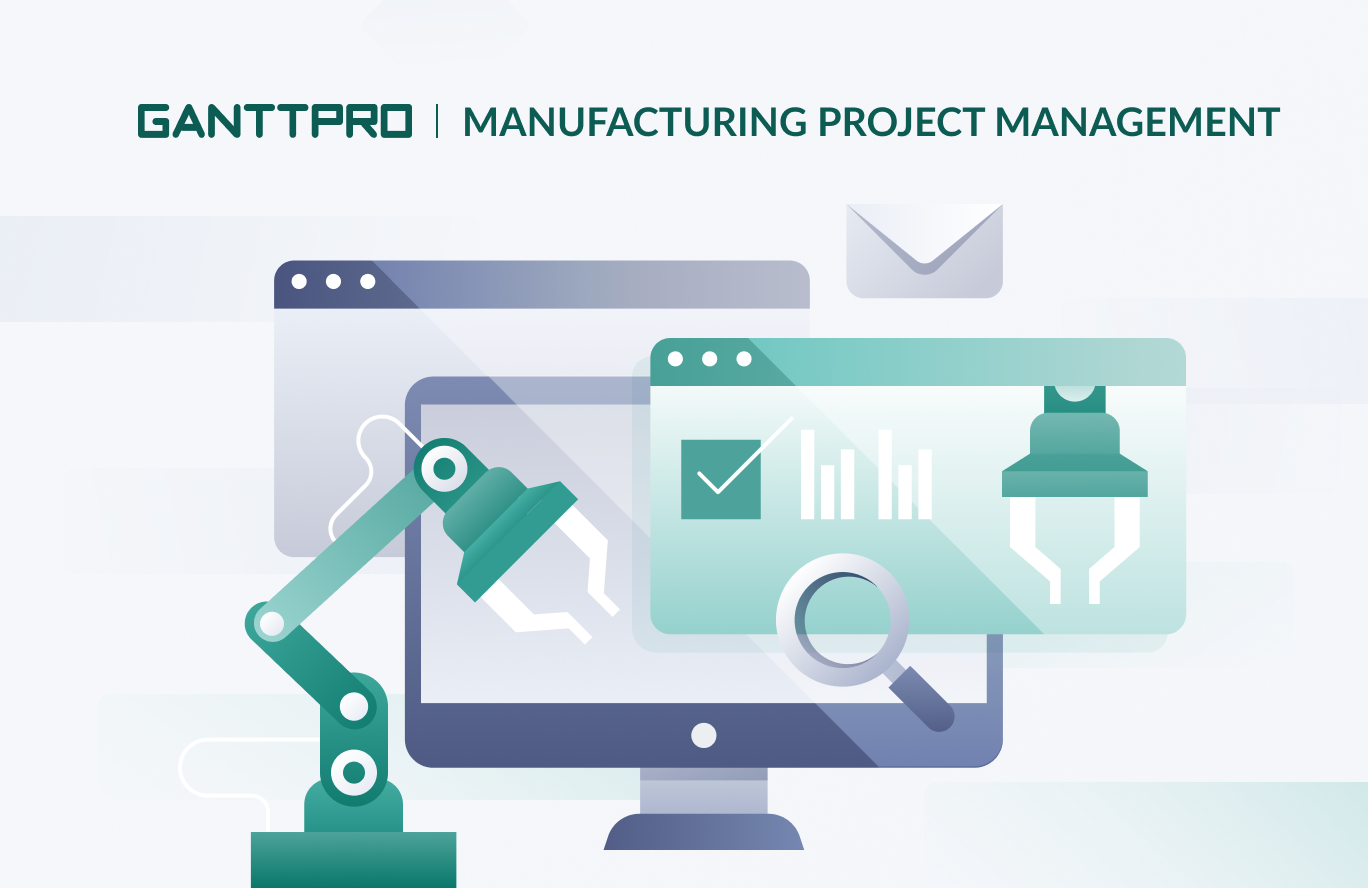
Audio version:
Manufacturing benefits greatly from effective project management. It’s critical to keep everything in order in this industry, where time and money are of the essence.
Streamlined manufacturing project management helps businesses increase profitability, improve efficiency, accelerate cash flow, and boost customer satisfaction.
Realizing the popularity of this topic, we’ve described the specific advantages of project management for the industry, helpful tips specific to manufacturing, and how professional software can help keep everything organized. You’ll also get illustrative project management manufacturing examples.
Contents:
- What is manufacturing project management?
- Benefits of manufacturing project management.
- Typical stages of project management for manufacturing.
- Project management tips for manufacturing projects.
- Project management manufacturing examples.
What is manufacturing project management?
Manufacturing project management is the series of processes related to planning, coordinating, and controlling specific projects within the manufacturing industry.
Organizations that deal with production or manufacturing take advantage of professional project management to reduce waste, improve risk management, and boost overall efficiency on production lines. It can involve managing timelines, resources, and budgets to achieve manufacturing-related objectives.
The key goal of project management in manufacturing is to ensure successful project completion while meeting quality standards and delivering them within the specified time, scope, and cost constraints.It is worth mentioning that the popularity of the sphere is not constant. Sometimes manufacturing causes increased interest, and sometimes it loses positions.
According to the data released by the U.S. Bureau of Labor Statistics, manufacturing lost 2K jobs in May 2023.
However, managers and specialists employed in manufacturing companies around the world don’t lose faith in the bright future of this industry.
Here’s what Scott Paul, the President of the Alliance for American Manufacturing, thinks about it:
There’s good reason to be bullish on the future of American manufacturing with factory construction booming, but we can’t overlook the current weakness in employment numbers. We look forward to advancing additional competitiveness measures that will ensure a strong future for American manufacturing.
In order to understand why the production sphere and project management in manufacturing will evolve in the future, let’s delve into their main advantages.
Obvious benefits of manufacturing project management
Efficient project management helps the manufacturing industry mitigate possible challenges and enables manufacturers to produce better products at the lowest cost and in the shortest time frames.
What reasons push manufacturers to implement the best project management principles and practices?
Below are the advantages of project management for manufacturing companies.
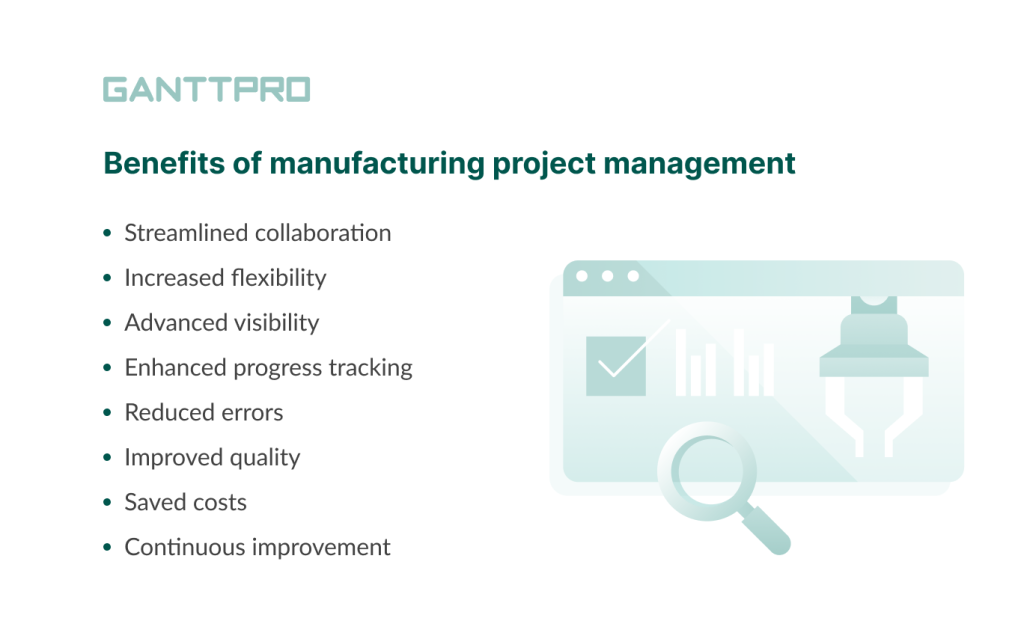
1. Streamlined collaboration
Improved project management enables better communication and collaboration among all stakeholders involved in manufacturing processes. It provides a single spot for sharing data that logically smooths the decision-making process.
2. Increased flexibility
The postulates and principles of Lean project management, on which manufacturing PM is based, enable production teams to work more flexibly while avoiding unnecessary activities in the process.
In Lean, these activities are often called “wastes”. It means that these steps don’t add any value to the production process.
Effective project management for manufacturing helps streamline production processes. It increases efficiency and leads to more quality outputs.
Remember, that eliminating excess processes will always give you more flexibility to react to unforeseen events.
3. Advanced visibility
Manufacturing projects may consist of multiple tasks and involve different departments. By sharing the joint approach to project management, manufacturing teams can have a better understanding of the progress of their projects. They can better reduce production costs and potential bottlenecks, and improve customer satisfaction.
4. Enhanced progress tracking
By applying traditional project planning tools such as a Gantt chart and a work breakdown structure, manufacturing teams can bring order into the processes and track the progress of their projects.
It allows them to identify the steps necessary to deliver the product and be aware of how to manage project delays in schedules.
5. Reduced errors and the lack of chaos
Streamlined project management in the manufacturing industry helps organizations faster reduce errors and organize all tasks and processes without chaos. After all, it ensures that all specific steps are completed correctly and on time.
6. Boosted quality
Ensuring quality standards is an essential part of any manufacturing project. Therefore project managers always strive to reduce the risk of errors, which results in improved product quality and satisfied clients.
7. Saved costs
Any organization that deals with manufacturing processes can reduce waste and increase efficiency with successful project management. It helps accelerate profitability and ensures resource optimization.
8. Continuous improvement
One of the key goals of manufacturing project management is to improve continuously.
Aiming to boost production processes, products, and tools utilization, project managers combine PM skills and practices with established manufacturing methods. It ensures increasing the effectiveness of processes that typically goes hand in hand with changes.
Changes may require time and resources. However, they are critical for business growth.
From the benefits of project management for manufacturing, it’s time to move on to the specific stages that form the lifecycle of a manufacturing project.
5 typical stages of project management for manufacturing
Like managing projects in other areas, manufacturing project management is typically broken down into consistent stages. They outline how a particular project will be managed.
Following these stages is a great way to manage your time and resources properly while making sure you efficiently reach your project goals.
The phases will be clear and consistent if you choose a reliable manufacturing project management tool, like GanttPRO.
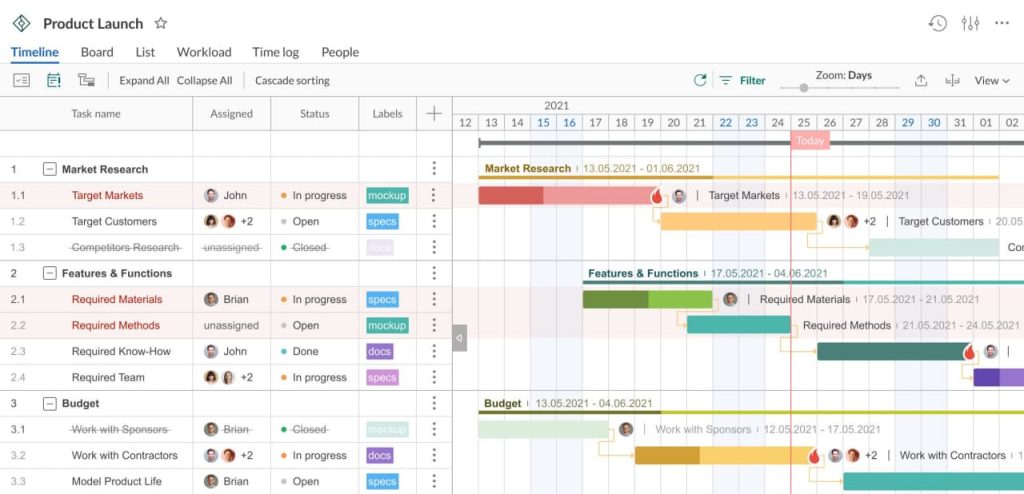
The professional Gantt chart maker keeps its leading position in the world of project management software as it comes with advanced features including:
- Project planning and scheduling.
- Task management.
- Time tracking.
- Resource management.
- Reporting.
- Budget management.
- Integrations
- Importing/exporting, and more.
Below’s the feedback from the manufacturing project management case study. Adam Hirsk, a Head of Product and Head of Research and Development departments at Pacvac company admits:
With GanttPRO, we manage our product projects from an idea through to development and production. All the details are well handled by the software.
How to apply the software during the phases of manufacturing project management?
Let’s go over each of the five stages.
1. Project initiation
Initiation and conception of your future project is arguably the most vital stage of the project management process. At this stage, project managers identify all project goals and research project feasibility. It’s often more about making some preliminary preparations to make sure you have everything you need before moving to the next stage.
It’s recommended to create a project brief that will outline the needs and purposes of your project in conjunction with the business case.
This stage is also important for getting all involved parties and stakeholders aligned on what’s to come.
You can move to the next stage without every detail documented, however, it’s better to agree on goals and intended outcomes.
Here you can take advantage of GanttPRO to get all your ideas and intents together and target the right team members to specific tasks.
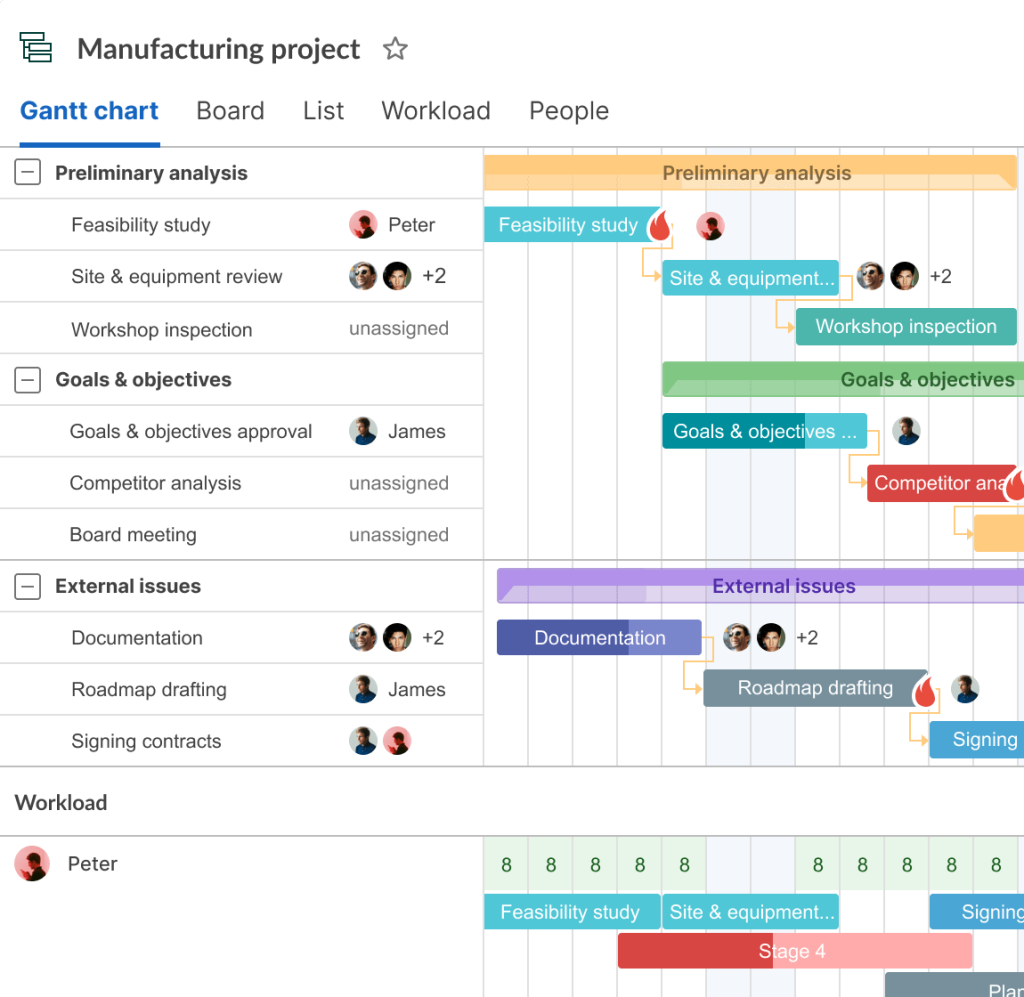
The gate at the end of this stage is the approval of your project that validates the approach and the strategy you want to apply.
2. Plans & schedules
Once you’ve defined what you want to achieve and how you can do it, it’s time to put together a detailed plan and visualize it on a handy project roadmap. The plan you outline at this stage will lead your team through the execution, performance, and closeout of your project management process.
Here’s what Gregg Profozich, the director of California Manufacturing Technology Consulting (CMTC), thinks about the role of planning in the manufacturing industry:
A strategic plan can serve many purposes but is typically ideal for established businesses interested in fueling new growth, expanding, or improving existing operations. Strategic planning is essential for many reasons, but it’s especially integral to protecting business continuity.
Choosing a manufacturing methodology that will suit your project is the next essential step.
Let’s say, the goal of your project is to eliminate waste in manufacturing processes. The principles of Lean project management will definitely assist.
In his other publication, Gregg Profozich shares his thoughts about Lean:
Satisfied customers are more likely to return and may be willing to pay a premium for products from suppliers that better meet their needs. Lean helps manufacturers focus on what customers expect by identifying what products, features, processes, and activities are of value to customers and seeks to remove or minimize everything else. At its core, Lean is about driving continuous improvement.
When generating a project plan, make sure you consider the following factors:
- Project scope.
- Project workflow.
- Project estimation.
- Roles and responsibilities.
- Project milestones.
- Approval processes.
- Communication plan.
- Risk management plan.
It seems that such an amount of information can hardly fit on one chart or within one roadmap. Fortunately, you can use GanttPRO.
The platform allows for generating and visualizing accurate manufacturing project plans and estimates in minutes.
Like many other projects, manufacturing projects can be long and complex. Therefore, managers often need to break up the work into smaller parts. There is no need for special skills and knowledge, as in GanttPRO WBS creator, you can easily place all your tasks and subtasks considering their hierarchy, dependencies, deadlines, and key project milestones. Adding required people and resources is also a cakewalk.
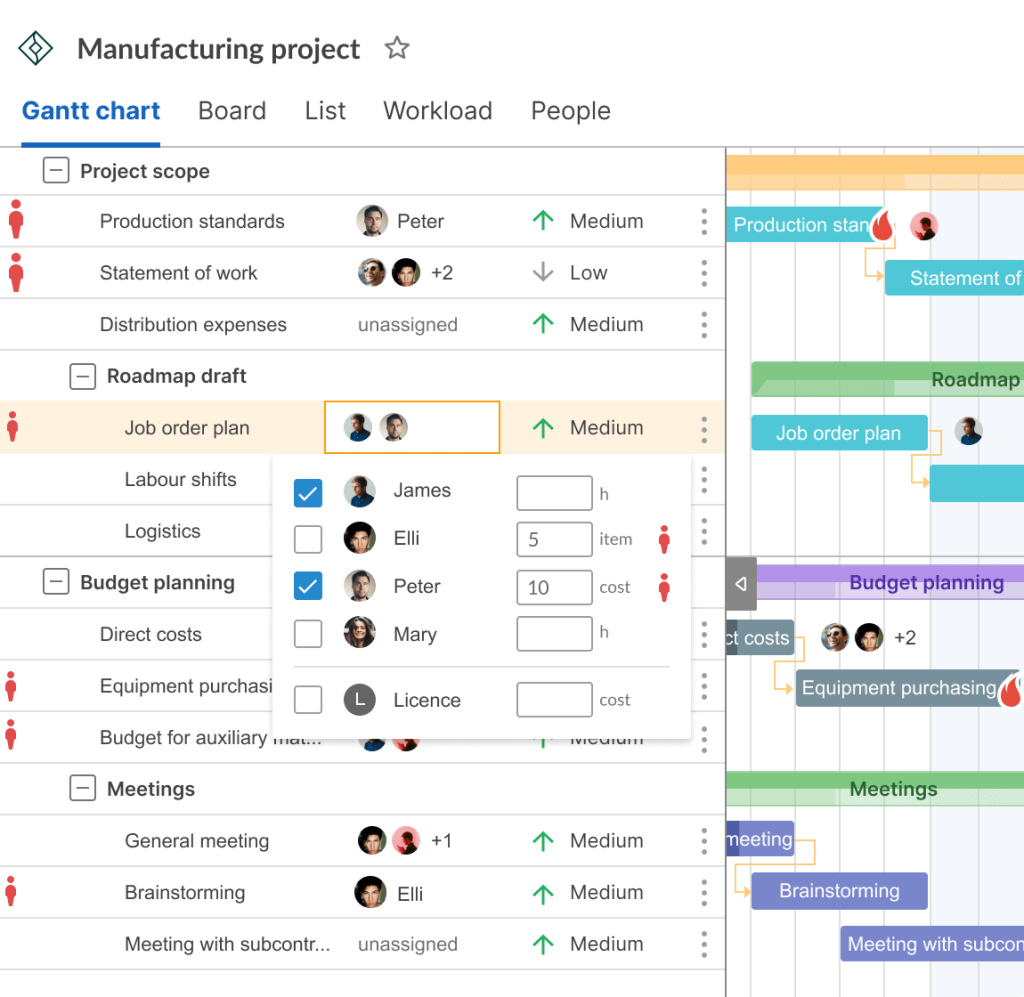
In GanttPRO, you can create and manage as many projects as you need with an unlimited number of tasks.
3. Execution
This stage is about making the project a reality. It is typically the longest phase in the project management process because it’s when the actual work is done.
Executing a project involves constant communication. A project team needs to make sure everyone knows what they’re supposed to do and when they’re supposed to do it. All team members should stick to the plan.
Manufacturing requires precision and accuracy in all processes, therefore it’s crucial to choose the right people and tools to complete the general plan. Here’s where GanttPRO also plays an essential role.
Capabilities to leave comments, use notifications, and add attachments even working outside the office make the software an extremely useful assistant for work in production.
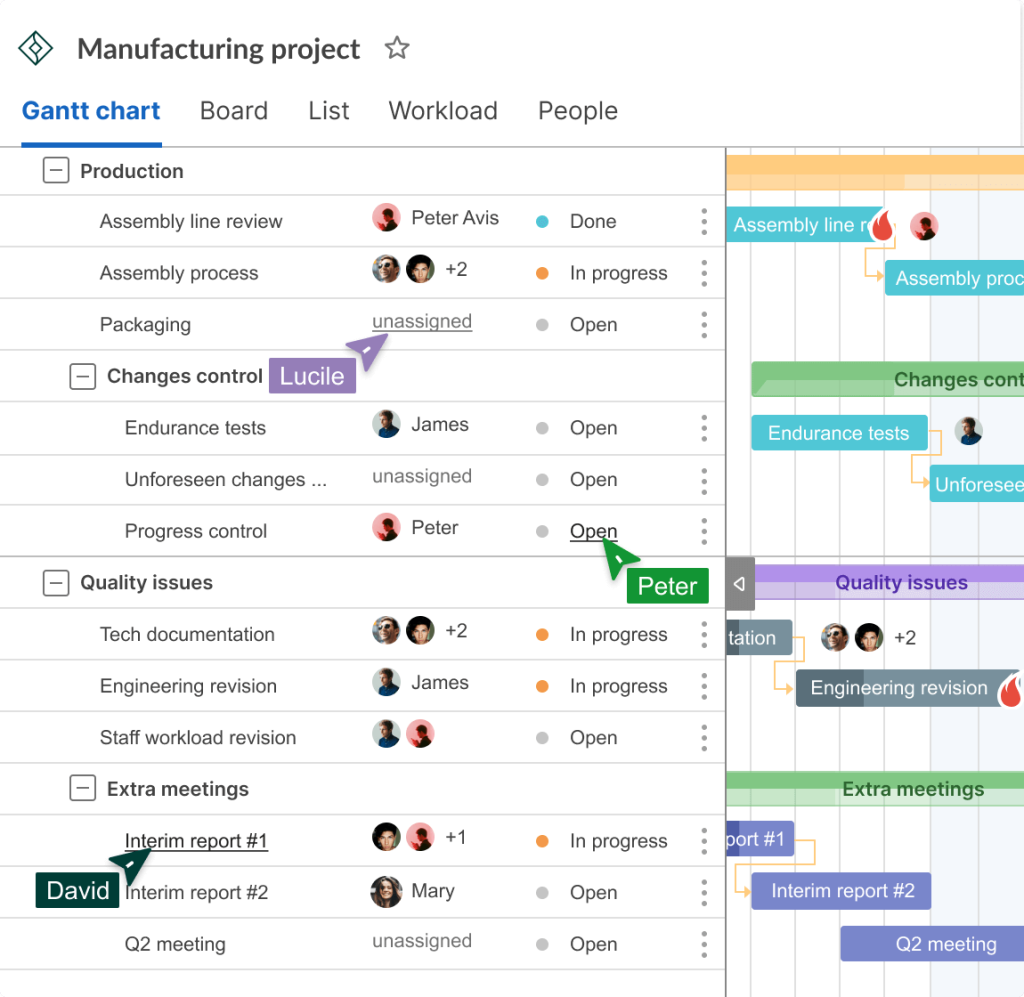
Additionally, you can provide your team members with special rights to view data.
GanttPRO allows for working with different account roles and project rights. You can provide your colleagues in the office or teams performing in a production workshop with different access to settings and features and customize work.
GanttPRO provides production teams with the professional set of project management features required for modern manufacturing project management software.
4. Monitoring & control
The fourth phase of the manufacturing project lifecycle means that it’s time to make sure you don’t lose momentum. This stage is predominantly about ensuring that all tasks and activities are performed correctly.
The role of a project manager here is to keep tracking everything in the project gets done safely and without causing any hiccups along the way.
During the project monitoring stage, you should keep an eye on:
- Resource planning.
- Budget issues.
- Team performance.
- Risk management.
- Quality control.
- Meeting management.
- Internal deliverable reviews.
- Communication, and more.
In GanttPRO, you can easily control all project phases and keep all parties in the loop. It’s possible to collaborate in one place without the need to switch from tool to tool.
Manufacturing teams all over the world take advantage of GanttPRO mobile apps available for iOS and Android, which allows them to control all project processes remotely. The apps simplify communication and help everyone stay on the same page.
5. Project closure
It’s time to wrap up. By this stage, your manufacturing project should be completed and all the parties should be happy with what’s been delivered, tested, and released.
During the closure phase, the team completes the steps required to close tasks, hand off the project to stakeholders, and analyze the big picture. They note incomplete tasks or possible equipment problems.
It’s also important to gather feedback and generate a detailed report for sharing it with all the people involved to improve your next projects.
Here’s how it can be implemented in GanttPRO.
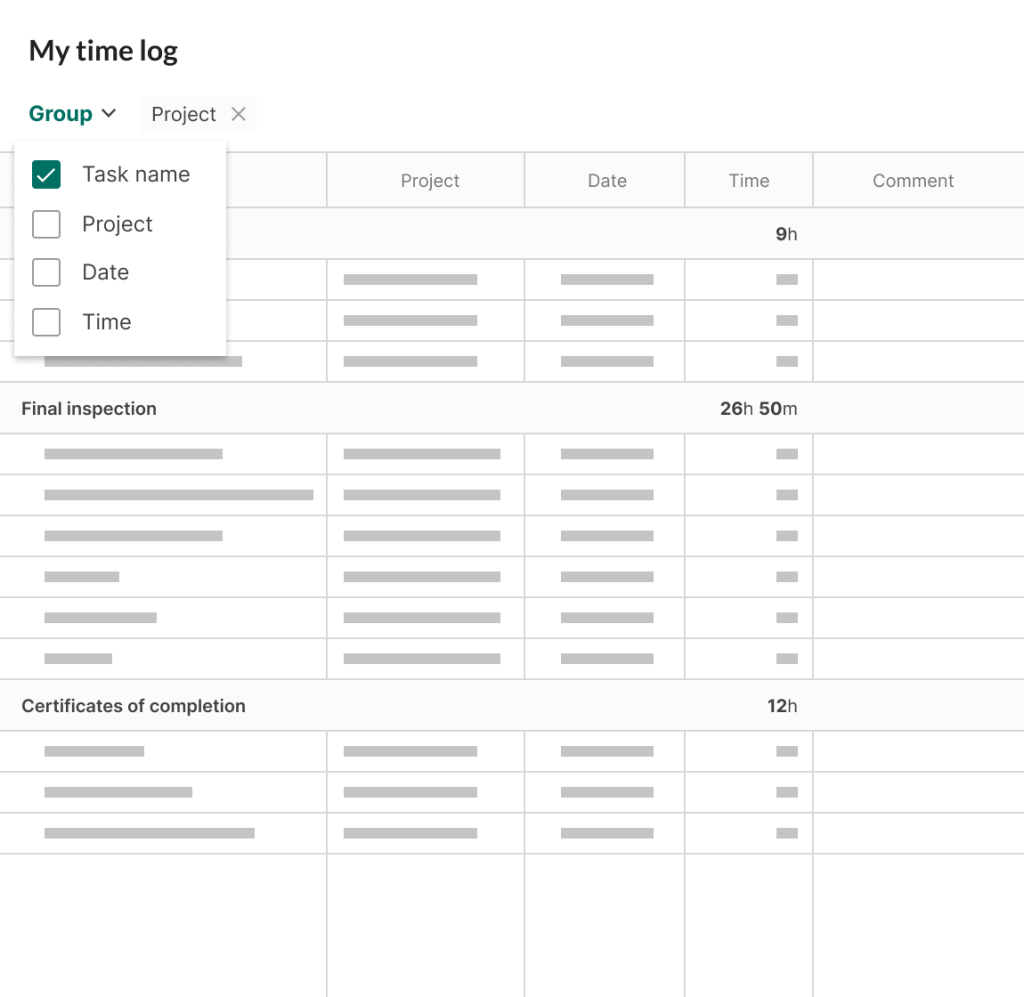
Since we’re describing project management in manufacturing and production specifically, it’d be great to double-check once again that everything you’ve implemented through your project is working safely.
Don’t hesitate to take the time to reflect on your work so that you can continue to be better.
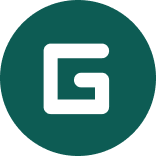
Professional manufacturing project management software
Plan, manage, and complete your projects on an online Gantt chart.
Sign up for freeProject management tips for manufacturing projects
Besides typical stages of managing manufacturing projects, there are additional secrets and tricks to maximize success when it comes to manufacturing processes. They are worth consideration, as sometimes even experienced project managers may lose their focus on how to manage and complete manufacturing projects correctly.
Let’s take a look at the key project management recommendations that are worth remembering throughout your entire career in the manufacturing industry.
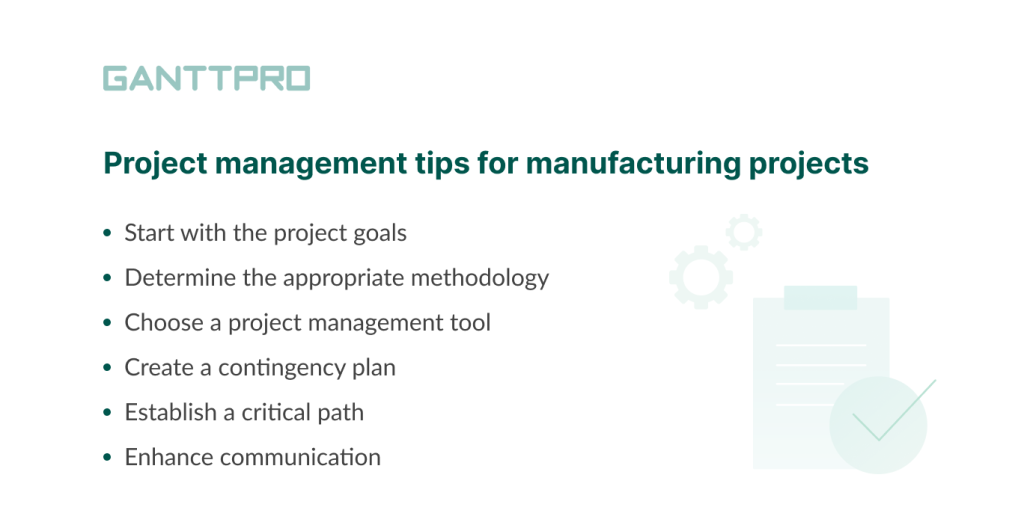
1. Remember that everything starts with the project goals
Don’t underestimate project goal setting, as any manufacturing process at any stage can go against the scenario because of a single wrong goal.
Such project requirements as budget, resources, and deliverables will help you set proper goals and lead to clear expectations from the very beginning of your project.
2. Determine the appropriate PM methodology
Having stated goals and desired project outcomes, you can choose the project management methodology that will work for you.
You can apply one of the famous methodologies like Agile, Waterfall, Kanban, or Scrum. However, there is no one-size-fits-all method when it comes to manufacturing. All approaches have their pros and cons, so try to pick up the one that will make the most sense for your processes and your team.
3. Make a reliable PM tool your best assistant
Modern project management software solutions help allocate resources, track materials and equipment, control scheduling, and analyze data to increase efficiency and reduce costs.
They automate many processes that previously had to be done manually.
This is how Uwe Kueppers, Manager of Consulting Services at Kalypso and EMEA board chairman of MESA, evaluates the impact of digital technologies and the adoption of automation:
Fast-growing digital technologies have enabled companies to adopt automation more readily and broadly than ever before. They enable a broader variety of data exchange and connectivity capabilities for different devices and applications which in turn allows for fast data access and process automation for different requirements within manufacturing.
Many online manufacturing PM tools offer free trial periods, so you have a chance to make sure the tool you’ve chosen supports key functionality and a high level of collaboration. For example, GanttPRO provides its users with a free 14-day trial.
4. Don’t forget about a contingency plan
Unseen circumstances and unexpected project delays do happen. Having a detailed risk management plan in place will help you prepare your team for potential risks and changes, keeping the project on track.
5. Consider establishing a critical path
When we talk about a critical path, we mean a sequence of activities that must be completed to achieve the project goals. They must be completed in the right order and within the right timeframes.
In the manufacturing sphere, it’s also important to remain proactive in managing critical paths.
You can easily find a critical path on a Gantt chart with GanttPRO and identify what tasks directly affect the project completion date. The platform even helps to make it easier as you can utilize any Gantt chart template available for this aim.
6. Avoid communication breakdown
Communication breakdown occurs when the information flow between project stakeholders is inaccurate or ineffective.
The reasons may relate to different communication styles or channels, language barriers, unclear roles and responsibilities, the lack of feedback and transparency, etc.
To prevent communication breakdown, take care of optimizing your communication methods, frequency, and responsibilities for each project group. Use clear language and encourage an open and honest communication style.
Let’s move on from the theoretical part of this article to clear practical examples. With their help, you’ll be able to deeply penetrate the depth of the process of project management for manufacturing companies.
Project management manufacturing examples
There are different types of manufacturing projects. Not all of them include developing new products. You can also find project management manufacturing examples focused on optimizing existing practices or implementing new ones. They can involve establishing a new assembly line, upgrading existing technology, or updating the supply chain management system.
We’ve found some interesting case studies in Plus Group – the company that offers solutions to a range of project needs.
One of their projects was completed in 2021. It was a new snack food product launch in the USA.
The company provided its engineering and design services to accommodate a new snack food product launch for one of the largest snack food firms in the U.S. The project required modifications and additions to the existing equipment.
Plus Group made sure the production of the new product went smoothly and the launch date was met. The client desired to coincide with the Super Bowl – one of the most popular days of the year for snack food providers.
Their project milestones included works on the new filling depositor, hydraulic power units, and new filling delivery chute.
Surely, your case of project management for manufacturing may have its own characteristics and unique features.
However, to bring you closer to a common understanding of such type of management, we’ve generated our own example of managing a manufacturing project – upgrading equipment and producing a trial batch of paper in a paper production company.
Company: Paper production company.
Project title: Adjusting a trial period of a full product delivery process with the new equipment.
Duration: August 1-30.
Parties involved:
- Project manager.
- Manufacturing engineer.
- Quality control engineer.
- Operation manager.
- Machine operators.
- Assembly line workers.
- Logistics coordinator.
- Maintenance technician.
- Supply chain manager.
- Health and safety officer.
Project overview: The result of this project should be the successful testing of the new equipment and the production of a monthly batch of paper within the trial period.
Objectives: Implementation of a new production system, identification of possible errors and malfunctions, paper testing, and receiving feedback from the control group.
Scope of work:
- Dismantle the old and defective equipment.
- Prepare the workshop area.
- Install the new equipment for paper production.
- Test the equipment.
- Produce the first batch.
- Produce the monthly batch of paper.
Task list:
- Approve the assembly working group.
- Approve the production team.
- Run the dismantled works.
- Clean the workshop.
- Approve the safety document.
- Install the new equipment.
- Start the 1st phase of testing.
- Start the 2nd phase of testing.
- Produce the trial batch of paper.
- Sign the order for the production of the new batch of paper.
- Calculate consumables.
- Produce the full batch and correspond to the order.
Project schedule:
- Start of dismantling works: August 2.
- Completion of dismantling: August 3.
- Workshop cleaning: August 4.
- Light repairs: August 4.
- Installation of new equipment: August 7.
- Installation of new lighting: August 7.
- Installation of additional components and related parts: August 8.
- 1st phase of testing: August 10.
- 2nd phase of testing: August 11.
- Trial batch of paper production: August 14.
- Full batch production: August 18.
- Сalculation of consumables: August 29.
- Project completion: August 30.
- General meeting: August 30.
- Control group feedback: August 31.
Here’s how it can be visualized in GanttPRO:
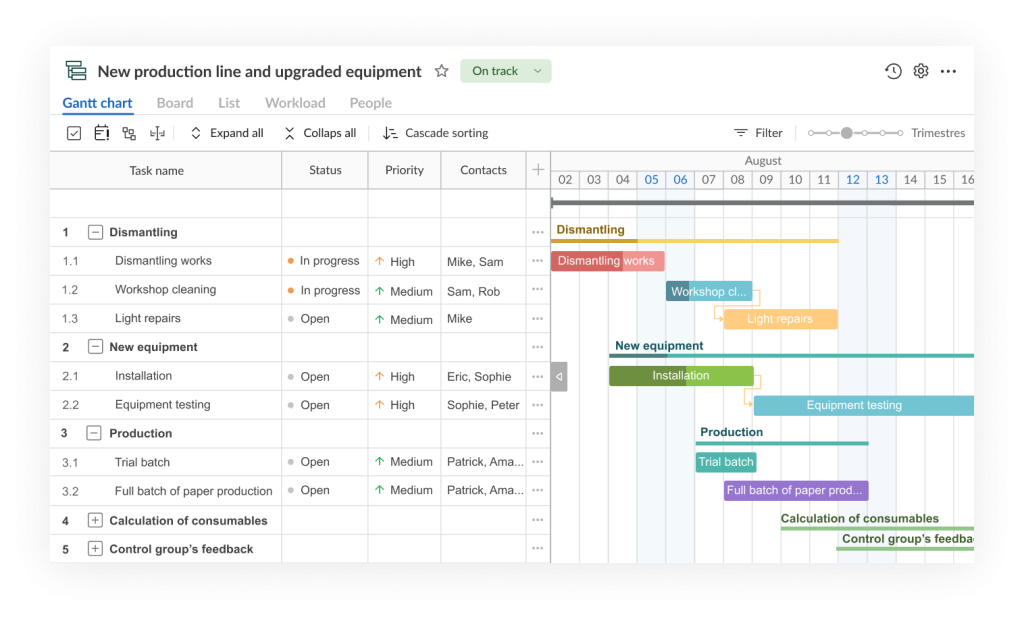
Project deliverables:
- The new line of high-tech equipment.
- New production team.
- Renovated workshop room.
- The first batch of paper produced with the new equipment.
- Optimized production plan.
Project management:
- Project manager: Patrick.
- Manufacturing engineer: Amanda.
- Quality control engineer: Sophie.
- Operation manager: Tom
- Machine operators: Eric, Brad.
- Assembly line workers: Mike, Sam, Rob.
- Logistics coordinator: Max.
- Maintenance technician: Peter.
- Supply chain manager: Shelby
- Health and safety officer: Julia.
Total budget: $32K.
Adoption plan summary: The new line of paper production equipment will be launched after installation and test period by October 1. A trial batch of paper will be used for the internal needs of the company and partners. The mass production of paper will start on October 1.
Put the manufacturing project management process to work with reliable software
There are no two identical manufacturing projects. Their details will vary depending on your particular needs, including the type of manufacturing process you use, the kind of goods you produce, or the kind of project you strive to complete. However, there are still many similarities that we can bring out.
The core benefits, consistent stages, recommendations, and bright examples of manufacturing project management will help you better understand the sphere and succeed professionally.
To make sure everything runs smoothly, you need a reliable project management tool. Don’t doubt to apply GanttPRO, which is designed to help you schedule, manage, and complete comprehensive manufacturing projects with passion.
No matter how complex your project is, the Gantt chart maker has everything you need to get it done quickly and efficiently.
Frequently asked questions about manufacturing project management
-
Project managers involved in the manufacturing industry play a crucial role in overseeing a project from initiation to completion. They typically have responsibilities like project planning, stakeholder management, resource allocation, risk management, budget control, quality assurance, schedule management, team leadership, change management, documentation, reporting, and more.
-
Examples of manufacturing projects may include not only developing new products but also cases focused on optimizing existing practices or implementing new ones. There are numerous examples of manufacturing projects across various industries, including automobile manufacturing, electronics, food processing, pharmaceutical manufacturing, aerospace manufacturing, textile manufacturing, renewable energy equipment, chemical manufacturing, and more.
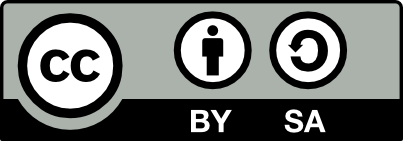